Advancing collaboration for advanced high-strength steels
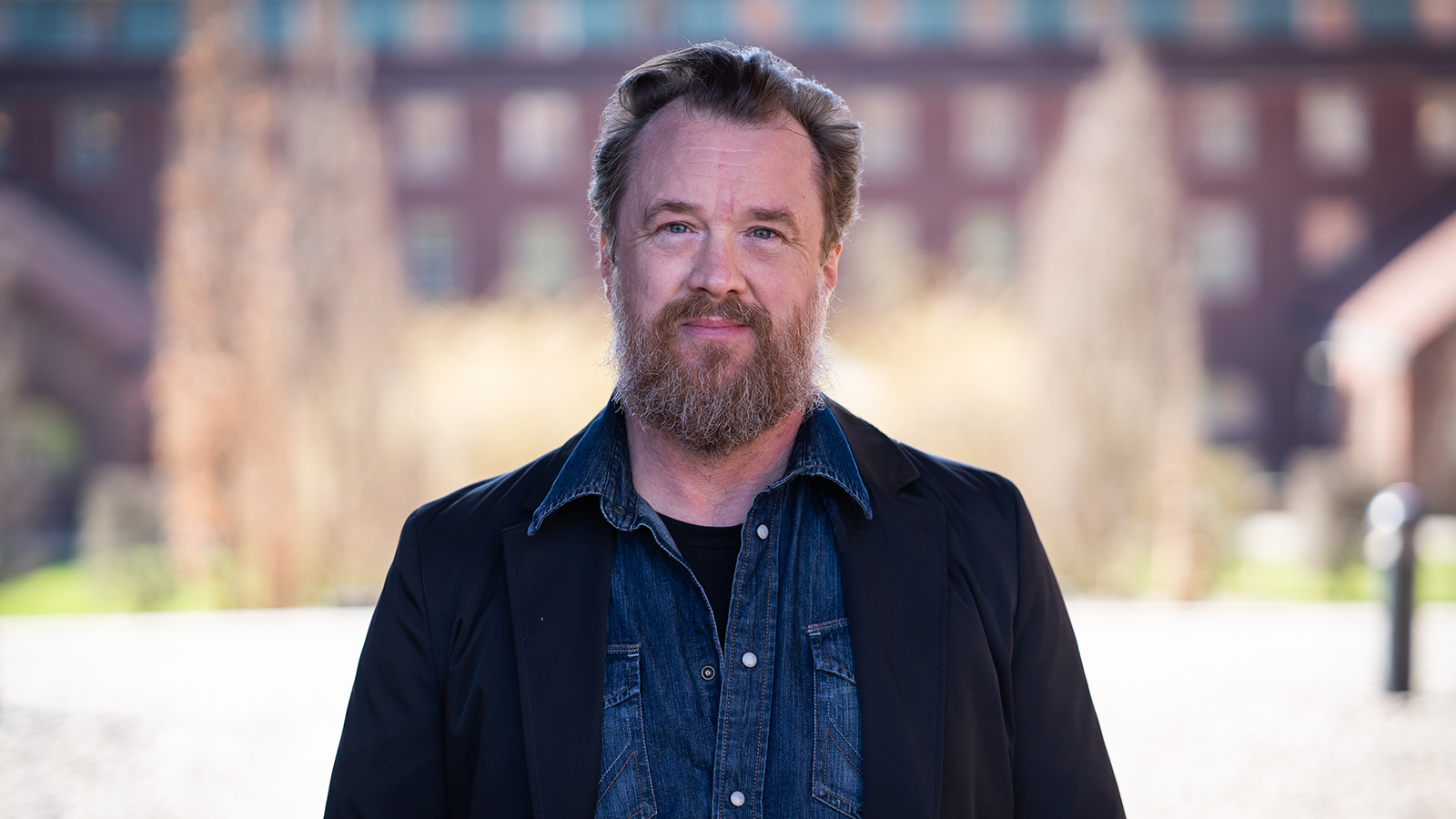
Henrik Sieurin earned his PhD at KTH. Now he’s back as an adjunct professor and expert in fatigue of the world’s most recycled material – steel. With a focus on collaboration for smarter solutions in the field, he divides his time between Scania and the Department of Materials Science.
Henrik Sieurin returns to KTH to contribute to expanded, cross-functional collaboration between the KTH and Scania, focusing on the mechanical properties of steel. As an expert in steel fatigue – particularly in the context of heavy vehicle production – he highlights the increasing demands placed on material durability:
“The fact that a truck today is expected to have a lifespan of up to two million kilometers places great demands on the durability of materials,” he says. “Fatigue cracks can occur at relatively low loads if the design is not smart and the right material is not chosen. To increase energy efficiency and load capacity, it is also important to design with lightweight in focus, which requires materials with high fatigue strength.”
The development of new advanced high-strength steels is ongoing.
“To succeed, it is crucial to understand the relationships between alloy composition, microstructure, and properties. For an end user like Scania, it is also important to understand how residual stresses, processing, defects, and surface finish affect the fatigue properties of a component,” says Henrik.
Since component design is affected by how well materials withstand long-term loading, Henrik would like to see more collaboration between material development and solid mechanics. Close collaboration between design, simulation (FEM), material selection, and testing/verification is essential to find the right balance between strength and weight.
“If a part is too weakly designed, it shows up first in simulation and second in component testing. Testing is expensive, so reliable simulation is extremely important, which places demands on the quality of material data and the understanding of it.”
Climate-friendly production
Henrik points out that the transition to more climate-friendly production needs to happen across the entire value chain. For Scania, this means that the requirement for green steel from 2030 will also apply to subcontractors.
“Close collaboration with open communication regarding climate goals, production processes, and emissions is crucial,” he says.
Standardisation and certification of the climate impact of steel products are other ways to increase sustainability in the industry, as is minimising the amount of scrap in generated during production and reusing any leftover material in a resource-efficient way.
“In a typical press shop within the automotive industry, only 50–70 percent of the steel is used, while the rest becomes scrap. It is high-quality scrap that, in a so-called ‘closed loop,’ can be directly recirculated back to the steel supplier for the production of new high-quality steel,” says Henrik.
What are the most important industrial perspectives you bring to KTH?
“Undergraduate education can hopefully become more inspiring and assignments more understandable with examples from ‘real life’. Something I missed during my studies was the connection to industry and how research and development is conducted at a company.”
“In research, I can contribute by identifying needs, limitations, and future technical challenges within my and adjacent fields. The combination of practical experience and theoretical knowledge creates better innovation.”
Text: Alexandra von Kern