High temperature experimental kinetics
High temperature experimental kinetics research is supported by well-equipped labs that contain a variety of customised and custom-built furnaces, thermogravimetric analysis, sessile droplet testing.
Conductivity furnace
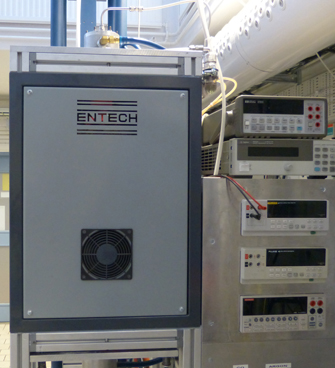
This furnace can be used to study the thermal conductivity of molten materials, such as slags, using the hot-wire method up to 1650 °C. The current (up to 5 A) needed to increase the temperature of the hot wire can be supplied using a source meter. The measured voltage change can be logged every 2.7 s by a voltmeter. The whole system is perfectly sealed to avoid infiltration by oxygen; without furnace opening the hot wire can be dipped in and pulled out of the sample. A cooling chamber is attached to the furnace for proper quenching of the heated sample. Different reacting and inert gases can be used with precise control of their flow rates, either in pure form or as gas mixtures. This makes it possible to use the furnace for equilibrium studies as well. The setup also can be used to measure the electrical conductivity of samples up to 1650 °C. It is possible to control the atmosphere with mixtures of Ar, H2, CO, CO2, N2 and H2O available. Samples may be quenched at any desired point in the heat treatment.
Viscosity furnace

This setup is rather unique in that it is capable of reaching and sustaining an operating temperature of 2100 °C. The furnace utilizes graphite heating elements which are argon shielded; at very high temperatures (>2000 °C), helium is used as the shielding gas. The body of the furnace is completely water-cooled, and water-cooled cooling chamber enables rapid quenching of a sample.
Alumina reaction tubes made out of alumina are used for temperatures below 1700 °C, while a special reaction tube made out of a molybdenum is used at higher temperatures. The setup is completely shrouded, enabling precise control of the furnace atmosphere and the oxygen potential. This system is very suitable for melting tests of slags and refractory materials, and for easily oxidized metallic melts. The most common use of the setup is for viscosity measurements; the quenching chamber enables measurement of apparent viscosity of multiphase mixtures. Electrical and thermal conductivity measurements for materials with high melting temperatures are also feasible with this apparatus.
Horizontal observation furnace
The main component of this setup is a horizontal electrical tube furnace An alumina reaction tube is sealed with o-rings by an internally water-cooled quenching chamber on one end, and on the other end with a water-cooled cap with a sealed quartz glass window. A carriage made of graphite holds the sample in the hot zone of the furnace, and a motorized screw drive enables the precise positioning and movement of the sample to reproducibly control heating and cooling rates. A gas train is used to prepare carefully controlled reaction gas mixtures. Argon is typically used in experiments, and it is first passed through a series of columns to remove water vapor and CO2, followed by three furnaces with copper turnings at 450 °C to reduce the oxygen partial pressure to very low levels.
Experiments may be performed at temperatures up to 1650 °C and contact angle measurements (sessile drop) may be performed at temperature. The precise temperature and gas mixture control allow equilibrium measurements to be carried out. Precise heating and cooling rate control also allow dynamic measurements to be taken.
Vertical Observation Furnace
The setup was designed for high temperature emissivity measurements. Therefore a large inner tube diameter (95 mm) was chosen with a short distance (400 mm) between the observation window and the sample. A tube resistance furnace with Super Kanthal heating elements is used to heat the sample up to 1650 °C. The alumina reaction tube is perfectly sealed to avoid infiltration by oxygen. Any possible gas composition controlled by mass flow meters can be supplied. The gases are cleaned with use of a gas cleaning system to keep the oxygen partial pressure as low as possible. After experiments the sample can be quenched within seconds and used for analysis. The setup is suitable for high temperature observation studies and non-contact measurements. The material of the observation window can be changed to any suitable material depending on the type of measurements.
Experiments may be performed up to 1650°C with high precision temperature and atmosphere control. It is possible to measure both emissivity and non-contact measurements at temperature. Both optical and infrared cameras are available for observational measurement. Samples may be quenched at any stage of the heat treatment.
Equilibrium furnace
The furnace is designed for equilibrium studies at high temperatures where long run times have to be employed. The furnace consists of a graphite heating element around an alumina reaction tube. The tube and the furnace are perfectly sealed against the atmosphere and against each other. In this way the gas composition inside the reaction can be precisely adjusted as desired. The reaction tube is connected to a gas train consisting of a gas mixer and two gas columns. The columns can be used for either cleaning of the gas or for control of the oxygen partial pressure. The samples are held by a pushrod connected to a lifting system. The lifting system can quickly raise the samples from the hot zone to the quenching chamber where the samples are rapidly cooled.
Experiments may be performed up to 1650 °C with high stability temperature and atmosphere control for longer-term experiments, up to 48 hours. It is possible to measure both emissivity and non-contact measurements at temperature. Both optical and infrared cameras are available for observational measurement. Samples may be quenched at any stage of the heat treatment.
Kinetic furnaces
There are two furnaces designed for high temperature kinetic studies.
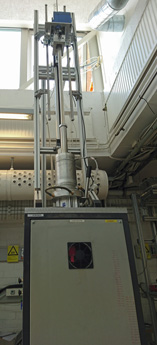
The first is equipped with Super Kanthal heating elements and can be operated at temperatures just above 1600 °C. The furnace is built around a 1 m long reaction tube of alumina with an inner diameter of 70 mm, which is sealed on both ends. Samples can be quenched by being lifted by the computer controlled lifting system into a water cooled quenching chamber made of aluminum. Extra quenching can be provided by simultaneously flushing the sample with inert gas while it resides in the quenching chamber. This furnace also has a second independent system that makes it possible to stir the sample under controlled atmosphere. The furnace offers a well-sealed experimental volume, allowing precise control of gas mixtures over long times (up to 72 hours). Short studies with stirring are also possible. The design allows a sample to be placed in the reaction atmosphere while cold and then be moved slowly into the hot zone in the same atmosphere. Lifing the sample out of the chamber provides rapid quenching. It is also possible to introduce additives into a molten sample and stir the mixture under a controlled atmosphere. The second furnace is a vertical resistance heated furnace equipped with Kanthal Super heating elements and an alumina reaction tube, enabling temperatures up to 1650 °C. The alumina tube being interconnected to water cooled aluminium chambers and the use of a computer controlled lifting system allows for fast cooling of the samples without withdrawal from the furnace. During quenching, the cooling of the samples can be enhanced by introducing extra gas directly into the quenching chamber. The furnace is sealed with O-rings which allows for a good control of the atmosphere in the reaction chamber. The setup allows for stirring of samples and addition of material under a controlled atmosphere making it suitable for both kinetic and equilibrium experiments.
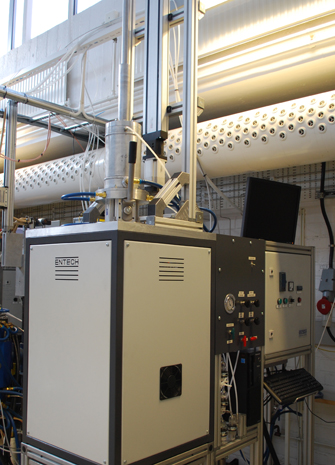
The second furnace is a vertical resistance heated furnace equipped with Kanthal Super heating elements and an alumina reaction tube, enabling temperatures up to 1650 °C. The alumina tube being interconnected to water cooled aluminium chambers and the use of a computer controlled lifting system allows for fast cooling of the samples without withdrawal from the furnace. During quenching, the cooling of the samples can be enhanced by introducing extra gas directly into the quenching chamber. The furnace is sealed with O-rings which allows for a good control of the atmosphere in the reaction chamber. The setup allows for stirring of samples and addition of material under a controlled atmosphere making it suitable for both kinetic and equilibrium experiments.
Thermogravimetric furnace
This setup is used for the study of any reactions involving weight change. The resistance furnace can be heated up to 1100 °C. The mass of the sample can be measured and recorded continuously by a high-precision balance. It is possible to introduce the samples from the cooling chamber (room temperature) into the high temperature zone of the furnace using a lifting system. Different reagents and inert gases can be used with precise control of their flow rate, either in pure form or gas mixtures. The system also allows rapid quenching of the sample.
Induction furnace
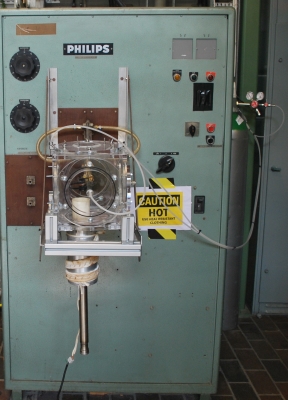
A water cooled copper coil connected to a 500 kHz, 60 kW power source enables stable levitation of metal samples of approximately 2 g in mass for more than five minutes, at temperatures above 1600°C. Around the coil a vacuum tight plexi glass box may be fitted to control the atmosphere. Gas inlets, both close to the sample and on the chamber wall, ensure the possibility to rapidly change the atmosphere in the direct vicinity of the sample, as well as the entire box. Quenching can be done in most liquids or on solids. The temperature is recorded with an optical thermocouple. The furnace is modular and so ancillary equipment can be added to or removed from the system easily.