3D Printing of novel Mg alloys aiming at production of patient-specific biodegradable implants
Background and challenges
In recent years, application of Mg alloys as biodegradable implants has gained substantial attention. Unlike titanium and stainless steel implants, Mg alloys can be gradually degraded in the human body, eliminating the need for a removal surgery. Good mechanical properties and degradation characteristics also make them superior to common polymers used in the human body. In the last decade, many magnesium alloys have been developed targeting biomedical applications ranging from maxillofacial reconstruction, to pediatric orthopedics, vascular stents, surgical clips, screws, plates, and bone-interfacing. Although magnesium has many advantages as hard tissue implant and tissue engineering scaffold material, application of magnesium is still limited in clinical applications due to its poor formability and rapid degradation in a high chloride environment and hydrogen evolution. Mechanical properties of the Mg alloys are of great importance since the designed Mg alloys should maintain their integrity and strength during the degradation process. Previous studies have investigated the effect of alloying, grain size and texture on the mechanical properties of the Mg alloys. As a novel alloying system, rare-earth (RE) containing Mg alloys have shown promising mechanical and corrosion properties through grain refinement and texture modification as well as excellent biodegradation properties. However, the use of these alloys as biodegradable implants is a new application which requires further study, especially from the alloy design approach.
Despite the benefits of the Mg alloys, their poor formability at room temperature has restricted their application by complicating their manufacturing. On the one hand, conventional manufacturing processes, such as rolling and extrusion, only offer products with simple geometrical shapes. Therefore, developing a manufacturing method for production of products with complex geometries is crucial. In addition, as the time is of crucial importance in medical treatments, development of a method for rapid production of products customized based on the patient status is of great importance. Additive manufacturing (AM) or 3D printing offers a mean for rapid production of complex customized products through a layer-by-layer production technique. However, employing laser melting for Mg alloys is faced with difficulties, due to intrinsic properties of Mg including high oxidation at elevated temperature and low boiling temperature. Therefore, the present production methods must be optimized for the Mg alloys to get the best results.
Purpose
The main objective of the present project is to design novel magnesium (Mg) alloys as well as to optimize the state of the art AM processes for fast production of Mg alloys with excellent mechanical properties. In addition, considering the extensive application of Mg alloys, the secondary objective is to provide a connection between material processing and biomedical properties through a multidisciplinary study, to develop new materials for production of biodegradable implants with enhanced properties.
Project plan
The project is divided into two phases, where phase 1 includes alloy development, optimization of the additive manufacturing process, and microstructural and mechanical characterization of the developed material. In this phase, thermodynamic calculations are used to find the most suitable alloying system for selective laser melting (SLM). Through computational fluid dynamics (CFD), SLM processing parameters are optimized by analysing the melt pool dynamics (figures below).
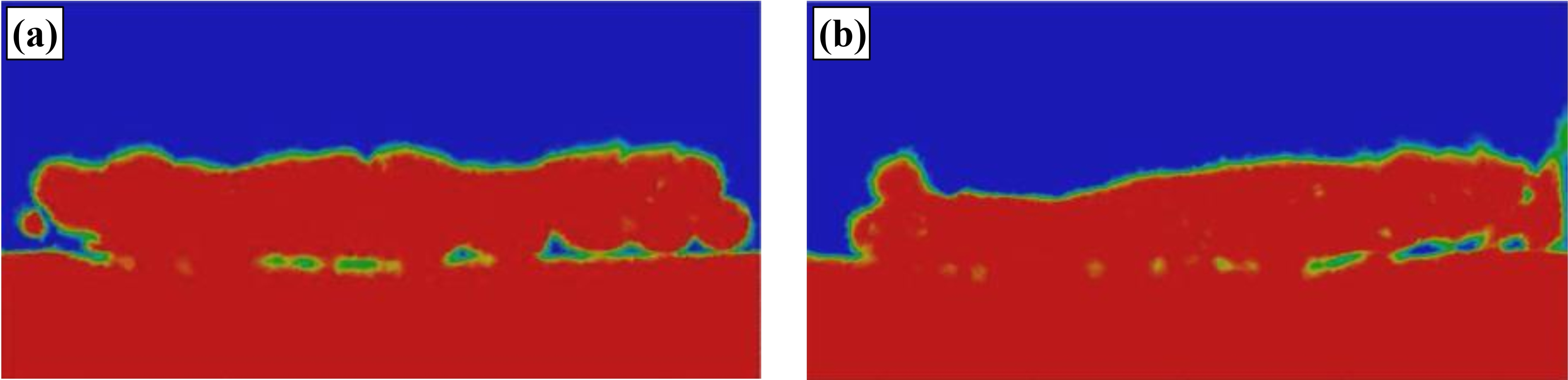

Phase 2 is aimed at evaluation of biodegradation properties of the material, especially evolution of mechanical properties during degradation, as well as a comprehensive modelling to predict the effect of processing parameters on the microstructural characteristics, mechanical and biodegradation properties. In addition, by the help of the advanced characterization methods, a better understanding of the relation of the microstructure-process-properties in the novel magnesium (Mg) alloys will be obtained.
Funding agency
Wenner-Gren post-doctoral fellow.
Beginning and end dates
2020-09-01 till 2022-09-01
Project contacts
More information
N/A