MMD PhD student project: Microstructural decay and fatigue crack nucleation from long term thermo-mechanical exposure
Background
When high strength bearing steels are exposed to repeated rolling contact cycles at high loads the material below the contact eventually displays changes in the microstructure and in the raceway a shallow groove will form resulting in a somewhat larger and more conform contact. An investigation of the material cross-section just below the contact through an optical light microscope revealed that the material volume directly below the contact had changed colour to a slightly different grey tone, illustrating material degradation.
The affected volume is small and comprises the highly stressed volume below the contact. During each over-rolling cycle a volume below the contact surface is exposed to a stress cycle consisting of increasing compressive normal stress in combination with a substantial shear stress. As the compressive stress increases the shear stress reaches a maximum and then it decreases back to zero at the compressive maximum, which coincides with the instance when the bearing roller is straight above the considered material volume. As the over-rolling sequence continues the normal stress is unloaded and a symmetric shear cycle is inflicted in the opposite direction to that during loading.
The microstructural change of the stressed material volume below a rolling contact is often characterized by dark etching areas after 10^5 to 10^8 cycles followed by white bands after 10^8 to 10^10 cycles for maximum contact pressures above 3 GPa. An example of microstructural decay as development of white etching bands and cementite decay is showed in Figure 1. It is of interest in the present project to develop a detailed understanding of the microstructural decay and to couple this with fatigue crack nucleation.
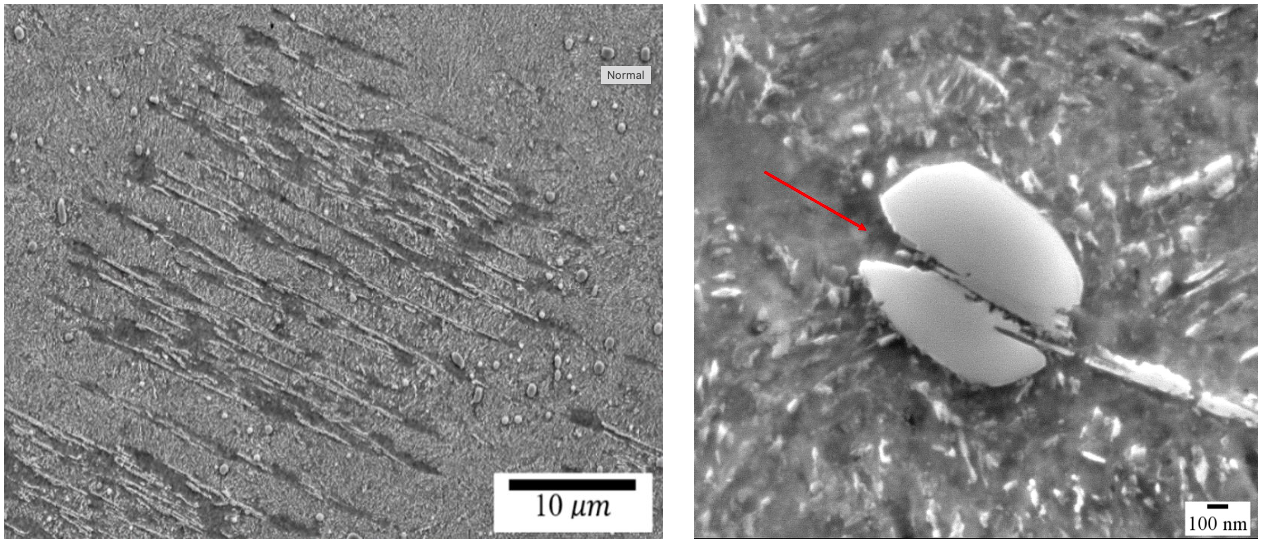
Purpose and aim
The purpose is to quantify microstructural decay of martensitic high strength steel from repeated long term thermomechanical exposure and the effects of the decay on fatigue crack nucleation and fatigue life. Fatigue is the most common failure mode of many steel applications, in particular bearing applications where crack initiation constitutes over 90% of the component life. Many fatigue cracks and fatigue failures in high strength steels are initiated by defects such as non-metallic inclusions or surface irregularities. Excluding surface roughness and material inclusions, there still remains the increasingly important question of crack nucleation in the material microstructure and the fatigue succeeding decay of the microstructure. Thus, the goal of the project is to develop a thorough scientific understanding of the microstructural decay of the material due to thermomechanical exposure and the underlying mechanisms of the succeeding fatigue nucleation. In particular, the project will focus on material decay and fatigue crack nucleation related to rolling contact fatigue in martensitic high strength bearing steels.
Project plan
The project work can be divided into phases. The first will be to quantify the microstructural decay found in the rolling contact fatigue experiments performed at Ovako. In parallel the literature will be searched for works on thermomechanical decay of martensitic and bainitic high strength steels. The third project phase aims at reproducing the decayed microstructure using independent loadings for specimens with homogeneous and macroscale material volumes. The forth phase comprises fatigue experiments on specimens with decayed microstructure. Micromechanical fatigue testing on the samples extracted from the decayed microstructure would be the next phase for detecting local strain-microstructure evolution. Finally, the local stress and strain distribution in the decayed and fatigue tested microstructure can be simulated using a grain structure and crystal plasticity models.
KTH and Ovako are the partners of this project.
Funding agency
Ovako through the MMD center.
Beginning and end dates
2019-06-18 till 2023-12-31
Project contacts
More information
N/A