HYBRIT will de-carbonize the steel industry
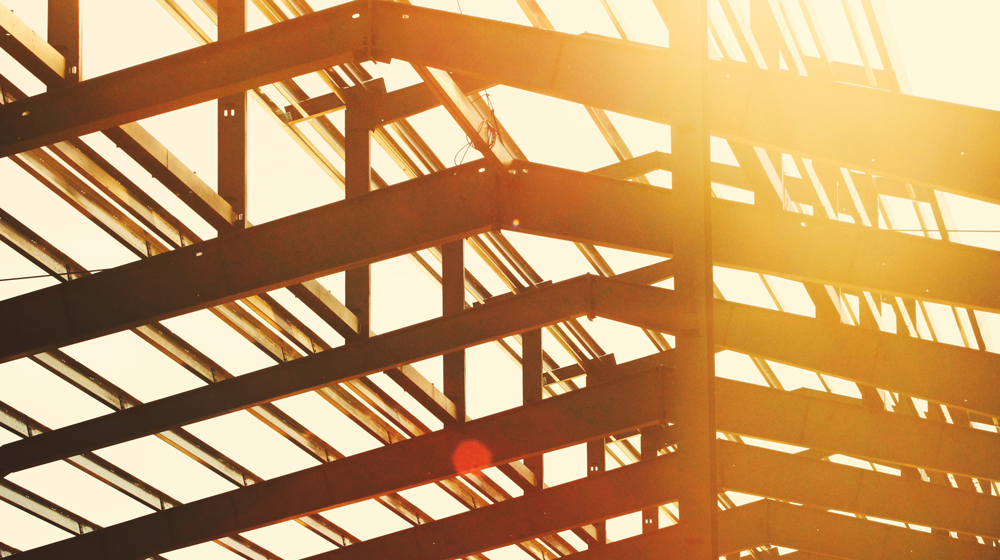
When the UN Climate Summit gathered the world's leaders in New York last fall, two Swedes were the talk of the town: Greta and "HYBRIT" - an initiative by SSAB, Vattenfall and LKAB that will make steel production fossil-free and substantially reduce CO2 emissions in Sweden. KTH plays an important role in what is called a revolution in steelmaking.
The steel industry is one of the highest carbon dioxide emiting industries. Swedish steel manufacturer SSAB accounts for about 10 percent of the emissions in Sweden, and globally, the steel industry accounts for about 7 percent. The demand for steel doesn’t seem to slow down - on the contrary. Living standards in the world are increasing and steel is an important enabler for building a society and its infrastructure.
“If we want to reach the climate goals, we cannot produce steel the way we do today. We have to do something drastic”, says Johan Martinsson from SSAB, who also has an employment as a researcher at the department of Materials Science at KTH.
And the revolution, initiated by the three industry giants, is called HYBRIT. As the name implies – Hydrogen Breakthrough Ironmaking Technology – it is about producing steel using hydrogen.
To make it happen, the initiative have turned to some of the sharp brains of KTH, where Johan Martinsson manage the metallurgical team. In total, four people from Materials Science work in the project. One of them is doctoral student Joar Huss, who explains KTH's role in HYBRIT:
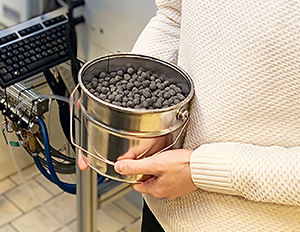
“There’s no other research group in Sweden with our profile that can do the type of fundamental research required in this project. KTH has a unique expertise in metallurgical research. We’re really good at high temperature experiments – thermodynamic phenomena but also reaction mechanisms”.
What makes steel production so high in CO2 emissions? The villain of the piece is the blast furnace, which produces nearly 1.5 tonnes of carbon dioxide per ton of produced steel. The blast furnace is used in the process of converting iron ore to steel. At a very high temperature and by adding fossil carbon, the oven reduces the iron ore to liquid pig iron. The residual product is CO2. This process accounts for about 90 percent of the CO2 emitted when producing steel.
Blast furnaces are based on a technology that is 1000 years old. Now, this process is innovated to be fossil free.
“The most accessible way is to replace the fossil carbon with hydrogen. Then the residual product becomes water instead of CO2”, says Johan Martinsson.
To produce hydrogen gas a lot of energy is required, energy that will come from fossil-free sources.
In order to cover all the skills needed here, the HYBRIT project has been divided into six research areas. KTH is involved in three of these: the reduction of the iron ore with the help of hydrogen, the steel production and how to produce and store the hydrogen, where researchers from other parts of KTH (CBH) are involved.
The research on energy and pelletization (converting the mine's ore into iron ore pellets) – are primarily managed by Vattenfall and LKAB, with the help of researchers from Luleå University of Technology and the research institute Swerim.
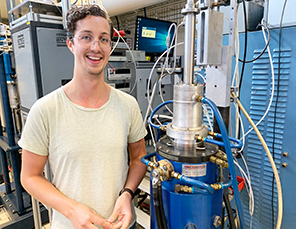
In a lab decorated with skulls and many warning signs at the department of Material Science, Johan Martinsson's project team has its base. Here they have built a blast furnace in mini format, that can experiment with temperatures up to 1100 ᵒC to reduce the iron ore to iron sponge with the help of hydrogen. Joar Huss works with the process that follows, and melts and cleanses the iron sponge from phosphorus and sulfur in his "Baby Blue" oven. Johan Martinsson works with another part of the purification process where foamy slag is currently in focus.
Further north, in Luleå, a pilot plant for a new type of oven is being built that will have hydrogen blown into it. This is what will replace the blast furnaces.
“It’s quite a piece hidden in a 50-meter high building, and it will produce 1 ton of iron sponge per hour”, explains Johan Martinsson.
Even though the first research package from KTH will be completed by 2021, Johan and Joar suggest that more collaborations are in the pipeline – like doing more research in the pilot plant.
“The HYBRIT project ensures that this type of knowledge remains at KTH. There is a stated ambition to educate people in this field and to inspire young people to study materials sciences”, says Joar Huss.
So when do we see the first sample of completely fossil-free steel? By 2026, a demonstration plant will be completed. Then the first fossil-free steel should be able to leave the gates of SSAB. The interest from potential customers is enormous, says Johan Martinsson, many industries want both fossil-free fuels and materials to get a green profile.
“Actually, the first fossil-free steel has already been manufactured. There was a full spread about it in Dagens Industri where the CEOs of Vattenfall, SSAB and LKAB posed with their own pieces made in KTH's lab. But we still haven't got them back”, Johan Martinsson laughs.
The steel making process
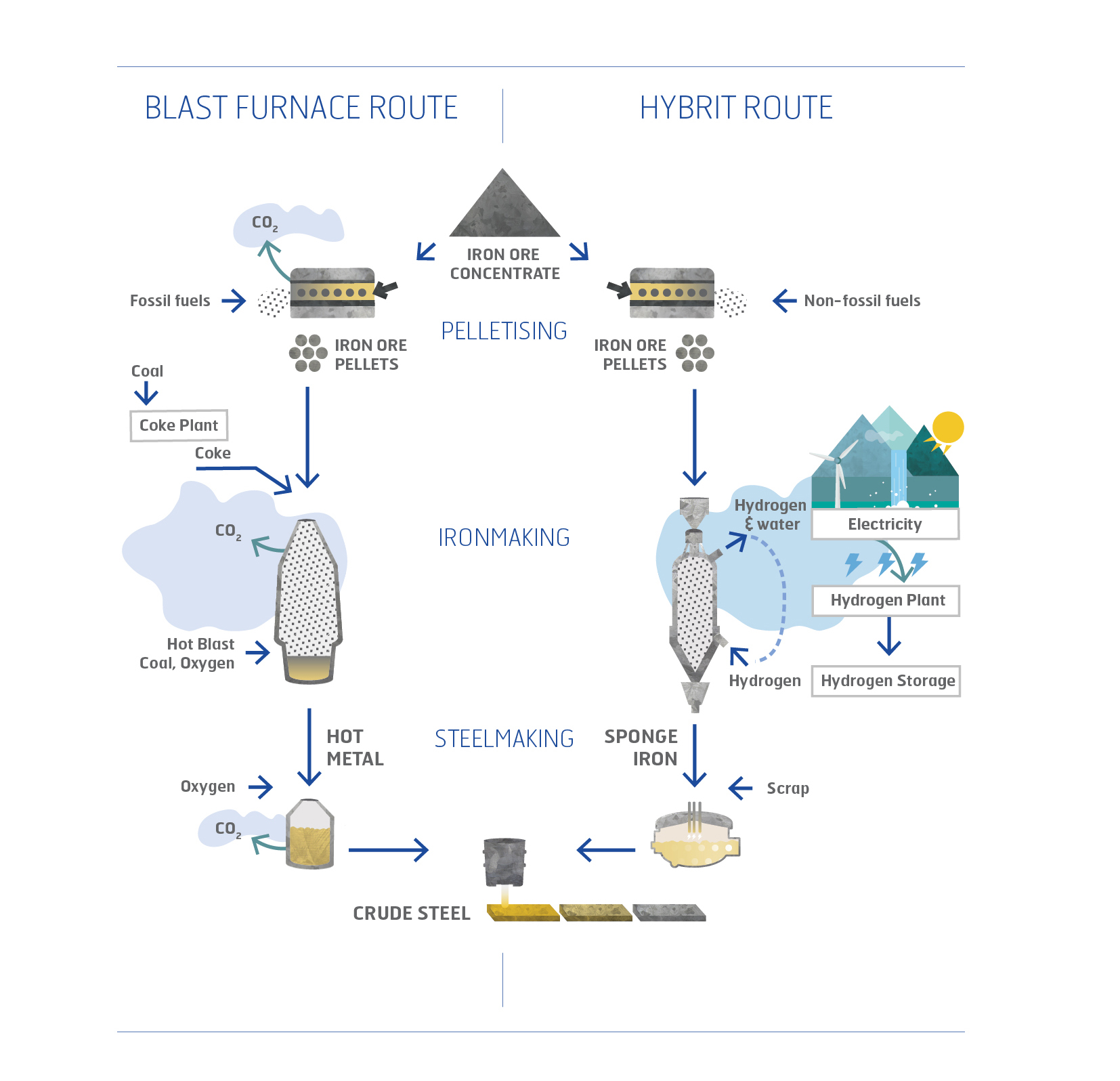
The ore-based steelmaking value chain starts at the iron ore mine. Iron ore is processed, and a product rich in iron oxides is produced in the form of pellets. At the steelmaking site, iron ore is converted to metallic iron by reduction of the pellets with coke in a blast furnace. The iron oxide and carbon then react to form CO2. Now in liquid form, the iron is further processed before a semi-finished steel product is cast.
In the case of HYBRIT, iron metal is produced by using hydrogen gas as the main reductant. But here the hydrogen reacts with iron oxides to form water instead of carbon dioxide.
Text & photo: Anna Gullers