Substitution of fossil Combination in Industrial high-Temperature processes by Advanced Electrical and plasma heating technologies
CITADEL
Effectively combating global warming requires a significant reduction in CO2 emissions. This poses enormous challenges, especially for the energy-intensive process and production industry, as this industry accounts for one third of total energy consumption. What is needed is intelligent electrification across all operational processes. Electrification has such a large potential impact on decarbonisation because it allows clean, renewable electricity to power processes that previously used emissions-intensive technologies (such as gas burners). This means that a process that previously produced high emissions can become absolutely emission-free when powered by renewable energy. The aim of the CITADEL project is to substitute fossil combustion processes with innovative electric technologies, such as electric resistance heating, microwave heating and plasma heating. Five use cases are considered, targeting the production of refractory bricks, glass and copper wires, preheating processes in steel production and the recycling of concrete. For these specific applications, appropriate demonstration plants have to be designed, built, tested close to the process and validated. This is supported by corresponding activities to provide suitable high-temperature materials and tools for instrumentation and effective process control. Challenges regarding a stable energy supply, electrical and thermal load management or intelligent energy management are simulated by means of numerical models. This includes corresponding risk assessments, e.g. with regard to possible time constraints in terms of a continuous power supply and the consequences of supply fluctuations for process safety. All demonstration cases will be evaluated by a life cycle analysis and with regard to the effectiveness in the reduction of greenhouse gases. The impact of the technical solutions developed here for the process industry will be assessed and strategies for scale-up and deployment will be elaborated.
Project partners:
- Helmholtz-Zentrum Dresden-Rossendorf (HZDR)
- Ceramica del Nalon S.A.
- Steklarna Hrastnik1860
- SIDENOR Aceros Especiales
- SIDENOR I+D
- C2CA Technology
- ASTA Elektrodraht GmbH
- Entch Energiteknik
- Fricke und Mallah Microwave Technology
- Kungliga Tekniska Högskolan (KTH)
- Jožef Stefan Institute
- IDENER.AI
- Politecnico di Bari
- Technische Universiteit Delft
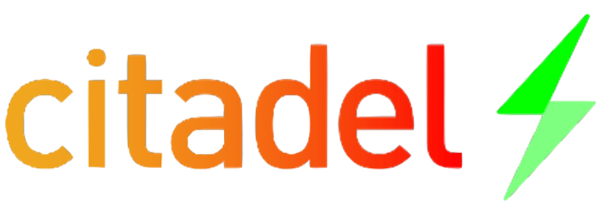
Funding Agency
Horizon Europe
Beginning and End Dates
1 January 2024 to 31 December 2027
Contacts
Other information
More information is available on the citadel website ( citadel ).
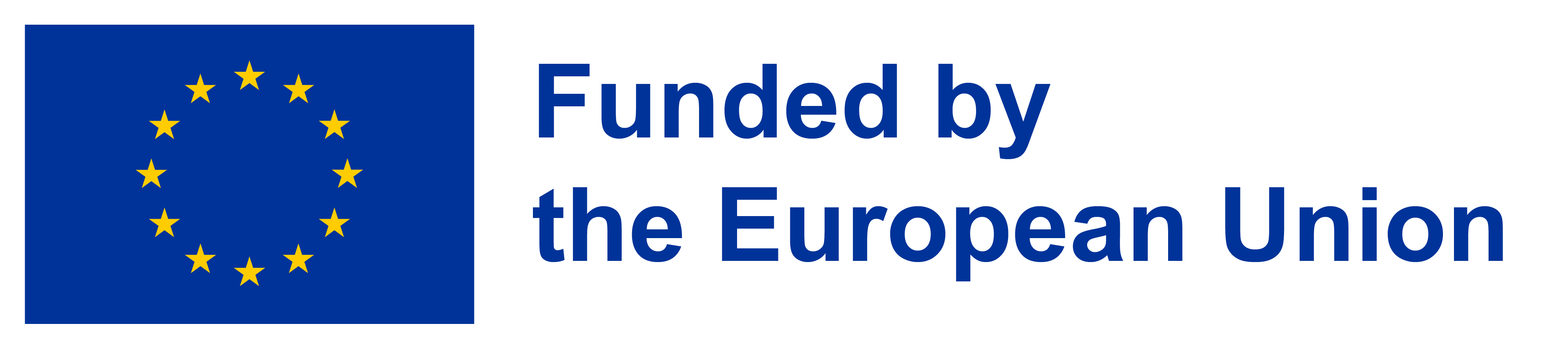