Casting
We focus on ingot casting, continuous casting, remelting and solidification in general. The field is like the rocket science of metallurgy, the cross-disciplinary field where physics and chemistry interplay at high temperatures where fluid mechanics, heat transport, thermodynamics, kinetics, process metallurgy and physical metallurgy intersect.
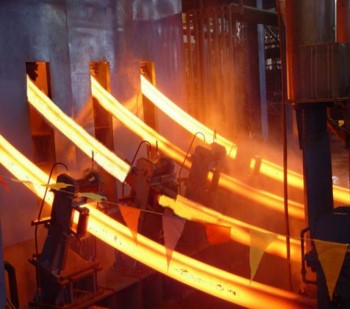
In our unit, we have an advanced group working with numerical modelling, long expertise with experimental studies, measurement techniques and plant trials. By operating on the scale from abstract theory to application with an overview of the process and its fundamental subsystems, we cover a wide range of Technology Readiness Levels and have a track-record of innovation and developemnt of ideas into industrial applications. Through external collaborations, we seek complementary infrastructure for experimental characterisation, pilot scale facilities and industrial problems with a fundamental cause.
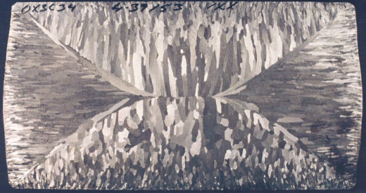
The future holds many openings to expand the use computational fluid dynamics coupled with chemical reactions during casting. Many high temperature material data is still lacking. This is, in part due to the difficulty of such measurements and/or the very high experimental costs. Here collaborations to use available equipment and shared infrastructure within the scientific community opens up these challenges to be tackled and solved. The pace of alloy development also increases the demand on process flexibility and rapid prototyping to find a usable operating window. Lab scale and bench scale tests that can be up-scaled to pilot or full scale are of high relevance to meet these demands. Furthermore, the digitalisation within the industry is now becoming a reality. Sensor technology, measurement techniques and quality of data needs to be standardised to reach the full potential of this revolution. That is our passion at KTH.